The use of stepper motors is an excellent choice. However, a key concern is step losses. Step losses can be prevented or corrected in most instances.
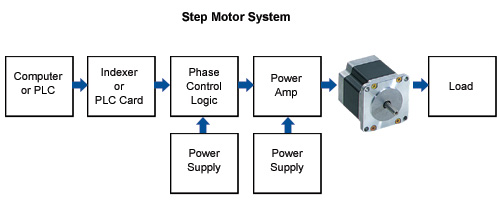
How to prevent step losses with Stepper Motors
Stepper motors operate open loop. When a stepping motor does not operate correctly in a specific situation, the common conclusion is that either the motor or the drive electronics is faulty. The motor selection and the choice of the driver are critical. However, other factors contribute to step losses.
The following points are important to examine for the analysis of step losses or non-operation in a methodical fashion across a variety of applications:
A. Stepper Motor Selection
B. Motion profile
B1. Start-Stop operation
B2. Trapezoidal profile
C. External commutation errors
D. External events
D1. Back driving
D2. Increase of the pay load over time
A. Stepper Motor Selection
The first task is to select the right step motor best price for the application. For the best selection, those basic theoretical rules have to be respected:
1. Select the motor based on the highest torque/speed point required by the application (selection based on the worst
case)
2. Use a 30% safety factor from the published torque vs.speed curve (pull-out curve).
3. Ensure that the application cannot be stalled by external events.
It is important to remember that a stepper motor does not operate like a DC-motor. There is no working point parameterization, and the phase current does not increase to overcome variations of load. As long as the speed vs. torque requirement of the application is within the specs of the motor, no problem will be encountered. If this requirement is out of the specs, the motor stalls (OK or NOT OK functionality). In any case, the current in the phases is not changing and adapting by itself to the situation.
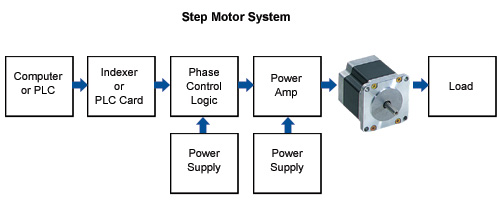
How to prevent step losses with Stepper Motors
Stepper motors operate open loop. When a stepping motor does not operate correctly in a specific situation, the common conclusion is that either the motor or the drive electronics is faulty. The motor selection and the choice of the driver are critical. However, other factors contribute to step losses.
The following points are important to examine for the analysis of step losses or non-operation in a methodical fashion across a variety of applications:
A. Stepper Motor Selection
B. Motion profile
B1. Start-Stop operation
B2. Trapezoidal profile
C. External commutation errors
D. External events
D1. Back driving
D2. Increase of the pay load over time
A. Stepper Motor Selection
The first task is to select the right step motor best price for the application. For the best selection, those basic theoretical rules have to be respected:
1. Select the motor based on the highest torque/speed point required by the application (selection based on the worst
case)
2. Use a 30% safety factor from the published torque vs.speed curve (pull-out curve).
3. Ensure that the application cannot be stalled by external events.
It is important to remember that a stepper motor does not operate like a DC-motor. There is no working point parameterization, and the phase current does not increase to overcome variations of load. As long as the speed vs. torque requirement of the application is within the specs of the motor, no problem will be encountered. If this requirement is out of the specs, the motor stalls (OK or NOT OK functionality). In any case, the current in the phases is not changing and adapting by itself to the situation.
No comments:
Post a Comment